- Explore our industry expertise
- Success stories
- GFT helps major automaker boost vehicle quality by migrating production floor to the cloud
GFT helps major automaker boost vehicle quality by migrating production floor to the cloud
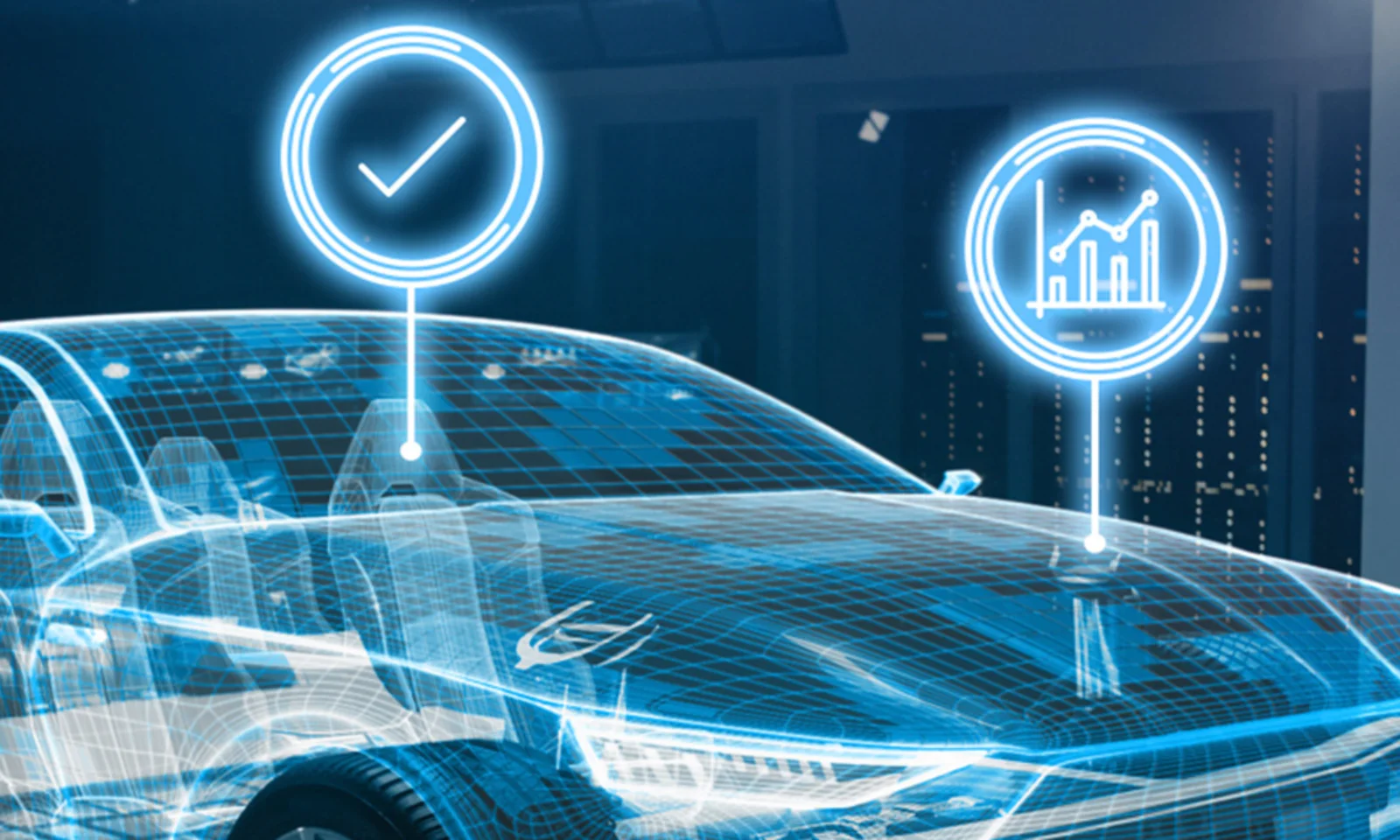
Migrating production floor to the cloud in less than six months
One single application providing analytics to support business processes
Using relevant data to reduce costs, downtime and improve quality
Challenge
Wrangling with disparate data
The U.S. auto manufacturer has made a bold commitment to shift more of its production to electric vehicles (EVs). In 2021, for example, it announced it would begin producing an electric version of its F-150 pickup, the best-selling vehicle in America.
Shifting from internal combustion engines to electric motors isn’t simple. The move changes the entire architecture of the shop floor. The higher level of electronics in cars, especially EVs, creates an opportunity to boost productivity and improve quality by enabling better communication among vehicles, facilities, and the manufacturing process during assembly.
The increased connectivity of the Internet of Things (IoT) produces vast amounts of data, but that data must be located, organized, and analyzed. In the auto-making process, data sets typically are spread among different vendors, parts-manufacturing facilities, and assembly plants. As a result, much of the data resides on vendors’ hardware, with on-premises data centers at various manufacturing plants, and on many different clouds. In addition, data are collected from sensors and other IoT devices on the production floor, but there is little consistency from one plant to the next.
In automaker's case, it wanted to aggregate its manufacturing data into a single platform that it could access from any location. U.S. auto manufacturer envisions an environment of seamless connectivity among its EVs, its people, and its manufacturing equipment.
Engagement
Digitizing the factory floor
GFT has deep knowledge in automotive and manufacturing, and it has worked closely for many years with Google Cloud, the U.S. auto manufacturer's preferred cloud provider. That enabled GFT to develop a cloud platform that could collect, aggregate, and synthetize manufacturing data from disparate sources onto a single application based on Google Cloud’s Manufacturing Data Engine platform.
GFT created data parameters, processed the collected information, and then used machine learning to develop dashboards and other data visualization interfaces for U.S. auto manufacturer and its suppliers.
For a test bed, GFT and the U.S. auto manufacturer selected a stamping plant that makes outer body panels for the F-150 and Transit commercial vans. The line produces about 900 parts per hour, or about 3 million panels a year. For each of those, the U.S. auto manufacturer sensors and other monitoring equipment track incoming materials, analyze assembly line operations, and collect images of each part produced by the line. The U.S. auto manufacturer hosted the image collection on Google Cloud, but the volume of data was overwhelming.
In a matter of months, the U.S. auto manufacturer had amassed 500 million data points that needed flexible and reliable storage. One of the first steps was working with the U.S. auto manufacturer to identify extraneous data that it didn’t need for the new application. GFT took the remaining data sets and defined operational and technical requirements, and then tested the system on the stamping line.
By processing and analyzing the stamping-line data, the U.S. auto manufacturer was able to spot variations in materials, control the stamping process parameters more effectively, and determine the output for better-quality parts.
Collecting all the data on a single platform allows the U.S. auto manufacturer to review data sets from different sensors. By comparing two sets of data from similar equipment, the U.S. auto manufacturer can monitor differences in performance, spot malfunctions early, and make repairs with less disruption to the production line.
GFT conducted the U.S. auto manufacturer pilot effort in about three months, and the entire rollout was completed in about six months.
Benefit
Using relevant data to reduce costs and downtime, improve quality
The pilot proved successful, and the U.S. auto manufacturer is implementing the platform across other factories. With the consolidated cloud platform, the U.S. auto manufacturer can create new applications based on access to more manageable and meaningful data than the company had before.
For example, with information collected from factory sensors, the automaker can better understand operating patterns and detect irregularities. As a result, it can target preventive maintenance efforts to ensure machines are repaired before they break down and that routine maintenance isn’t done unnecessarily on equipment that’s working properly.
The platform also will allow the U.S. auto manufacturer to better measure the quality of body panels, batteries, parts, and other components before they’re installed. By making any necessary adjustments early in the process, the U.S. auto manufacturer can improve the quality and reduce defects, recalls, assembly line stoppages, and other costly corrections.
"Ultimately, the platform is addressing a very common need across all manufacturers, which is that all this information is being produced, but the data isn’t being used to its full potential. We took all the native core cloud components and configured them for ingesting and managing manufacturing data to produce greater insights and operating efficiencies."
Awards
OUTSTANDING PERFORMANCE
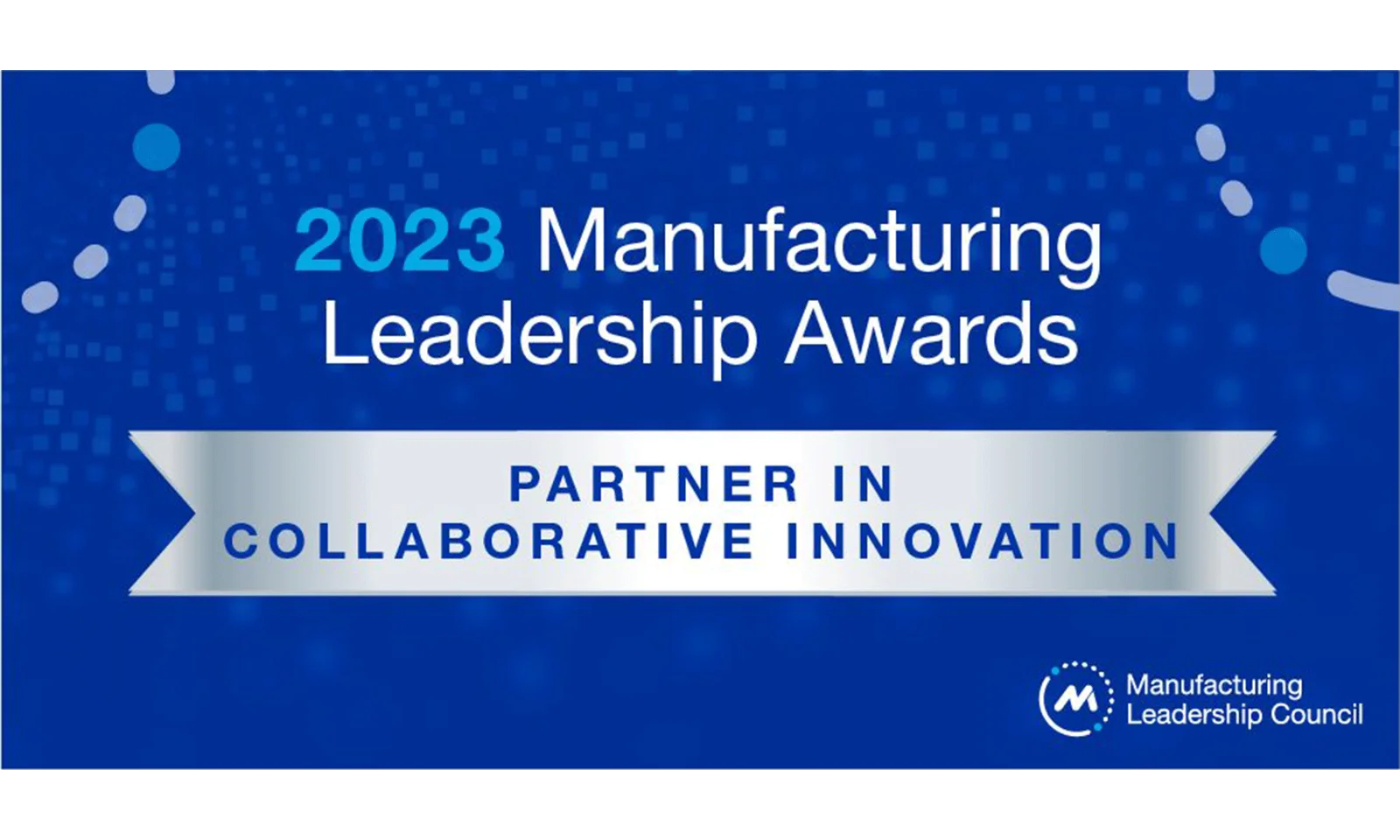
Download - just one click away
-
Success story
Using the Google Cloud Manufacturing Data Engine solution, GFT, brought a digital transformation to the automaker’s shop floor in less than six months.
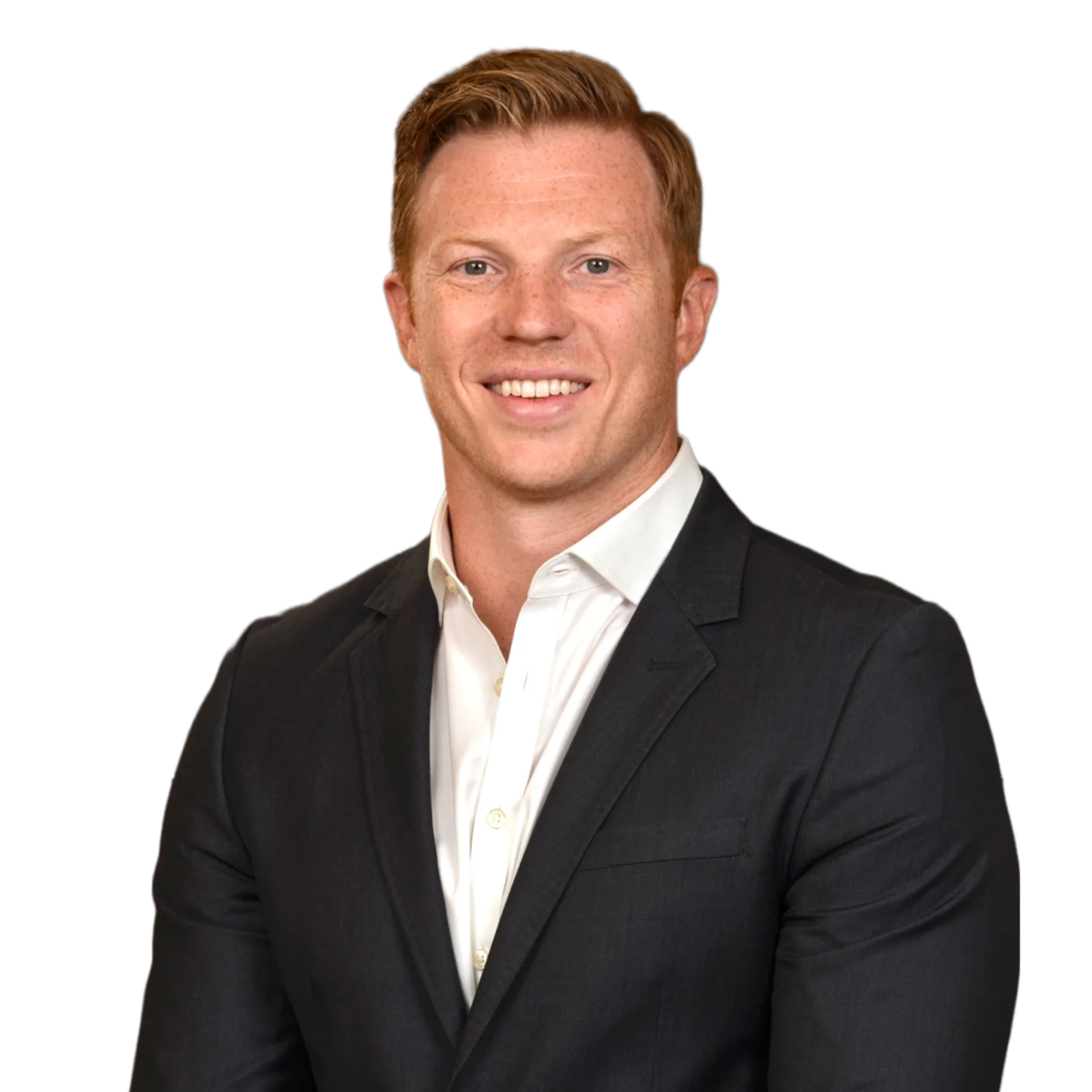